Audi Q7: Repair Information
General Repair Information
The highest level of care and cleanliness along with tools
that function properly are required to ensure a proper and
successful transmission repair. Of course the general safety
precautions also apply when carrying out repair work.
A list of general instructions that apply to multiple repair
procedures throughout the repair manual are summarized once here
under the "Components" section. Refer to
→ Chapter "Components". They apply to this repair
manual.
Safety Precautions and Test Procedures
- Repairs done incorrectly on the rear final drive 0D3 "Sport
Differential" could cause the final drive to malfunction.
- Testing, assembling and servicing must be performed by
qualified personnel only.
Correct Oil Level
- Make sure the rear final drive is filled to specified oil
capacity. Refer to
→ Chapter "Capacities".
- Fix any leaks on the rear final drive, for example, on the
sealing surfaces or the seals. The oil can leak out through the
holes between the left -arrow 1- or
right -arrow 2- chamber and the
rear final drive.
- Rear final drive malfunction.
- Do not drive the rear final drive if there are leaks or
insufficient oil.
- Leaks on the rear final drive must be corrected.
- Fill the ATF and/or gear oil if the levels are low. Refer to
→ Chapter "ATF Level, Checking, 0D3 Sport Differential"
and
→ Chapter "Gear Oil, Checking Level, 0D3 Sport Differential".
- Only use ATF or gear oil available as a replacement part.
Refer to the Parts Catalog.
- If the leaks cannot be repaired, then the rear final drive
must be replaced.
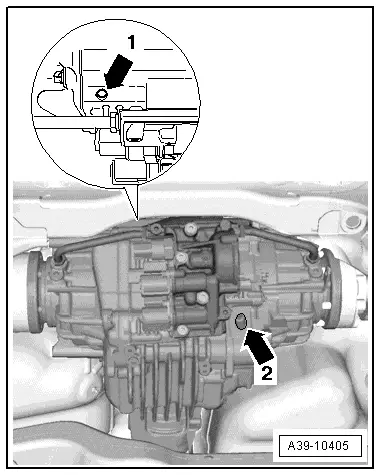
Rear Final Drive Performance
- Transmission control malfunction.
- Always maintain all specifications when replacing
transmission components. Only by doing so assures the
performance and the response characteristics of the rear final
drive 0D3 "Sport Differential".
Replacing Transmission Components
- When replacing the AWD Control Module -J492-, the adaptation
values for the transmission mount (for example clutch wear, oil
ageing) must be transmitted with Vehicle Diagnostic Tester
otherwise the performance of the rear final drive will be
impaired.
- When replacing a chamber or the complete rear final drive,
the clutch classification must be entered again in the AWD
Control Module -J492-. Refer to Vehicle Diagnostic Tester. If
the clutch classification is not performed in the AWD Control
Module -J492- then the rear final drive performance will be
impaired. When replacing a chamber, the classification
identification on the rear final drive housing must be made
unrecognizable. The identification of the new classification is
made on the new chamber housing.
- Do not place the removed rear final drive on any of the
components from the hydraulic control unit (for example, clutch
valves). This could damage the components.
Replacing the Oil Pressure/Temperature Sensor -G437- and/or
Oil Pressure/Temperature Sensor 2 -G640-.
- The identity of the sensor in the AWD Control Module -J492-
must be adapted. Refer to Vehicle Diagnostic Tester after
replacing the Oil Pressure/Temperature Sensor -G437- or the Oil
Pressure/Temperature Sensor 2 -G640-.
- Do not replace both the Oil Pressure/Temperature Sensor
-G437- and Oil Pressure/Temperature Sensor 2 -G640- at the same
time because a valid sensor identity is needed for the rear
final drive classification to the AWD Control Module -J492-. If
the both sensors are replaced at the same time, the AWD Control
Module -J492- will interpret this as the rear final drive is
being replaced. By doing this, adaptation values in the control
module will be erased and the performance of the rear final
drive will be impaired.
- If both the Oil Pressure/Temperature Sensor -G437- and Oil
Pressure/Temperature Sensor 2 -G640- must be replaced due to
mechanical damage, for example, if the connector housing gets
damaged, then this must be performed in two steps. After
replacing the first sensor, the identity of the must be adapted
in the AWD Control Module -J492-. Refer to Vehicle Diagnostic
Tester. Do the same for the second sensor.
- If both the Oil Pressure/Temperature Sensor - G437- and Oil
Pressure/Temperature Sensor 2 -G640- must be replaced at the
same time due to an electrical fault, then the clutch
classification must be entered into the AWD Control Module
-J492-. Refer to Vehicle Diagnostic Tester. Additionally the ATF
must be changed. Refer to
→ Chapter "ATF, Draining and Filling".
Torque Displacement, Checking
After the following work the function
22- Checking the torque displacement must be performed:
- Working on the rear final drive wiring
- Working on the valves: AWD Clutch Valve -N445- and AWD
Clutch Valve 2 -N446-.
- Working on the hydraulic control unit
Vehicle Lift Mode, Vehicles with Air Suspension
Activate the lift mode before lifting the vehicle on a two-column workshop
hoist (when there is no weight on the wheels). Refer to
→ Suspension, Wheels Steering; Rep. Gr.00; Repair Information; Wheel Bearing at
Standard Vehicle Height, Lifting Vehicles with Air Suspension.
Special Tools
Refer to the Special Tools Catalog for the complete list of special tools
used in this repair manual.
Components
Rear Final Drive
- Allocate bolts and other components according to final drive
code using the Parts Catalog.
- When replacing the rear final drive, check the oil level in
the rear final drive and fill if necessary. Refer to
→ Chapter "Gear Oil, Checking Level".
- Capacities and specifications. Refer to
→ Chapter "Capacities".
- Clean the contact surfaces when installing mounting brackets
and waxed components. Contact surfaces must be free of wax and
grease.
- Thoroughly clean the connection points and the surrounding
area before loosening.
Driveshaft
- The attached driveshaft can only be separated from the
transmission if it is completely removed.
- Always remove or install the driveshaft horizontally from
the transmission output shaft.
- Always store and transport the driveshaft when it is fully
extended.
- The driveshaft can be bent all the way to the center joint
without force. Bending the joint forcibly all the way can damage
the center joint and/or the protective boot.
- If the driveshaft is separated only from the rear final
drive, the driveshaft must be tied up or supported. If
necessary, the driveshaft can be bent as far as the end stop of
the center without force.
- Pay attention to the tightening sequence for the driveshaft
bolt on the rear final drive. Refer to
→ Fig. "Driveshaft to Rear Final Drive - Tightening Specification and
Sequence".
Should there be complaints (noise, vibration), do the
following before replacing the driveshaft:
- Remove all the driveshaft bolts from the rear final drive.
- Tighten the driveshaft with new bolts according to the
tightening sequence. Refer to
→ Fig. "Driveshaft to Rear Final Drive - Tightening Specification and
Sequence".
- Oil, Environmental and Disposal Regulations
- Handle ATF, transmission fluid and other oils with care.
- Dispose of drained fluid properly.
- Follow the legal, environmental, and disposal regulations.
- Follow the instructions listed on the fluid packaging.
O-Rings, Gaskets and Seals
- O-rings, gaskets and seals must always be replaced.
- After removing the seals, examine the contact surface on the
housing or shaft for burrs resulting from removal or for other
signs of damage.
- Thoroughly clean the housing separating surfaces before
assembling.
- Lightly lubricate the O-rings before inserting to prevent
the rings from being crushed during assembly.
- Lightly coat the seal on the outer diameter with oil before
installing.
- Fill the space between the sealing lips
-arrow- halfway with Sealing Grease
-G 052 128 A1-.
- The open side on the shaft seals faces the fluid to be
sealed off.
- After replacing the seals, gaskets and O-rings check the
gear oil level. Refer to
→ Chapter "Gear Oil, Checking Level".

Circlips
- Do not stretch the circlips.
- Always replace damaged or stretched circlips.
- The circlips must rest at the bottom of the groove.
- Replace the adapter sleeves. Installation position: the slot
-A- should align with the line of
force -arrow-.
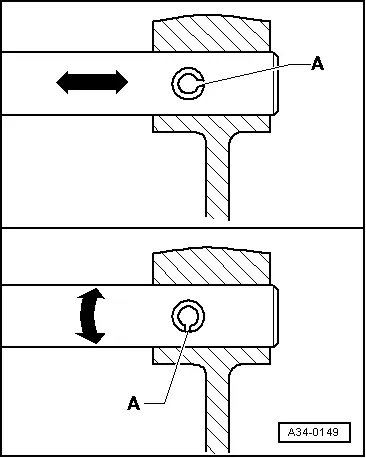
Bolts and Nuts
- Always loosen or tighten bolts and nuts on covers and
housings diagonally.
- Parts which are particularly sensitive must not be tilted
and must be loosened or tightened diagonally in stages.
- The tightening specifications given apply to unoiled bolts
and nuts.
- Always replace self-locking bolts and nuts.
- Clean threads of bolts that were applied with locking fluid
using a wire brush (does not apply to driveshaft bolts: these
must be replaced). Then insert the bolts with Locking Fluid -AMV
185 101 A1-.
- If self-locking bolts were installed or if regular bolts
were installed with locking fluid, then the threaded holes must
be cleaned, for example with a thread tap. Otherwise there is
the risk that the bolts could break off the next time they are
removed.
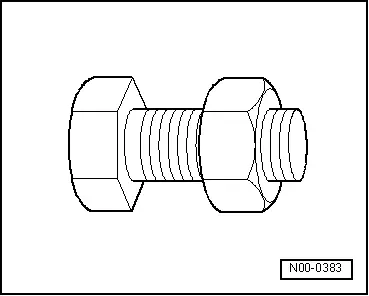
Contact Corrosion
Contact corrosion can occur if inadequate fasteners (bolts,
nuts, washers, etc.) are used.
For this reason, only fasteners with a special surface
coating may be installed.
Furthermore, all rubber or plastic and adhesive are made of
non-conductive materials.
If there are doubts about whether parts can be used or not,
use new parts. Refer to the Parts Catalog.
Note:
- Only original replacement parts are recommended. They are
checked and are compatible with aluminum.
- The use of Audi accessories is recommended.
- Contact corrosion damage is not covered under warranty.
READ NEXT:
Component Location Overview - Electrical Components
1 - AWD Control Module -J492-
Component location. Refer to
→ Fig. " AWD Control Module -J492- in the A4".
Additional work afte
SEE MORE:
Note
The Passenger Side Front Airbag Crash Sensor -G284- is
removed and installed the same way.
Removing
WARNING
Follow all safety precautions when working on
pyrotechnic components. Refer to
→ Chapter "Safety Precautions for Pyrotechnic
Components".
- Disconnect the
Fuse Panel F -SF-, Removing and Installing
Removing
- Remove the left luggage compartment side trim panel. Refer
to
→ Body Interior; Rep. Gr.70; Luggage Compartment Trim Panels;
Luggage Compartment Side Trim Panel, Removing and Installing.
- Disconnect the connectors -2