Audi Q7: Wiring Harnesses, Repairing
Note
Observe general notes for repairs on the vehicle electrical
system. Refer to
→ Chapter "Vehicle Electrical System, General Repair
Information".
Airbag and Belt Tensioner Wires, Repairing
In addition to the general repairs on wiring harnesses, the
following methods and instructions must be observed for repairs
on airbag- and seat belt tensioner wires:
WARNING
- The airbag and seat belt tensioner system can fail.
- Faulty repairs performed on airbag and seat belt
tensioner system can lead to malfunction in passenger
protection.
- When performing repairs on airbag and seat belt
tensioner wiring harness, use only terminals, connectors
and wires designated for it. Refer to the Parts Catalog.
Note
- Air bag wires and the safety belt tensioner wiring harness
may repaired only with the Wiring Harness Repair Set -VAS1978B-
and previous versions.
- Observe general notes for repairs on the vehicle electrical
system. Refer to
→ Chapter "Vehicle Electrical System, General Repair
Information".
- A maximum of two repairs may be performed when repairing
wires of airbag- and seat belt tensioner system. Repairs
increase the electrical resistance in the wire and may trigger
malfunctions in the system On Board Diagnostic (OBD).
- When repairing wiring harness of airbag- and seat belt
tensioner system, the crimp connectors must always be
heat-shrunk to prevent corrosion.
- Do not wrap the repair point again into the vehicle-specific
wiring harness and mark the repair point quite visibly with
yellow insulating tape.
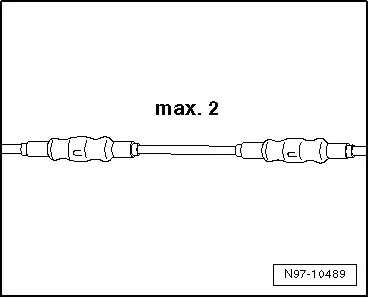
- Repairs in the area of the airbag or seat belt tensioner
should be performed a maximum of 30 cm from the next connector
housing. Together with the identification via yellow insulating
tape, this procedure makes it possible to obtain a quick
overview of previously performed repairs.
- Wires to the deploying units (airbags) have a wire-twisting
with a length of lay of 20 mm +- 5 mm in series production. This
length of lay is guaranteed via the norm part numbers for wire
pairs in series production and must be observed strictly for the
repair lengths of twisted wires.
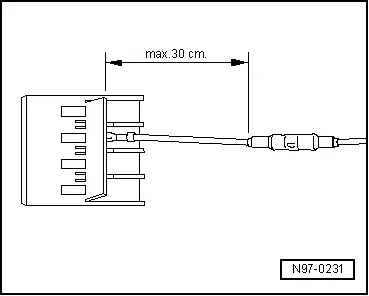
- During repair work, wires to deploying units (airbags) must
have the same length. When twisting together wires
-1 and 2-, length of lay of A = 20
mm +- 5 must be strictly observed.
- While doing this, no section of the wire, for example, in
area of crimp connectors -arrow-,
may be greater than B = 100 mm without twisting of the wires.
- Repairs are to be documented in the Audi Service Plan under
"Space for workshop entries" with a short commentary of scope of
repairs, workshop stamp and signature.
- Any warranty claims to Audi AG are void for repairs on
airbag wiring set which were not performed using original
replacement parts and Wiring Harness Repair Set -VAS1978-.
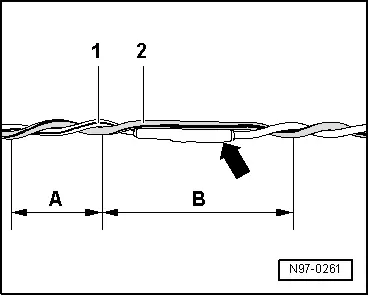
Repairing CAN bus Wires
- Unshielded, twisted two-wire lines -1
and 2- with a cross section of 0.35 mm
2 or 0.5 mm2
can be used as CAN-Bus wiring.
- Repairs on CAN-Bus wires can be performed with repair wire
with matching cross section and also with twisted wires
"green/yellow" or "white/yellow" from the Parts Catalog.
- When repairing CAN bus wires, both wires must be same
length. When twisting together wires -1
and 2-, the lay length of A = 20 mm must be observed.
- While doing this, no section of the wire, for example, in
area of crimp connectors -arrow-,
may be greater than B = 50 mm without twisting of the wires.
- Wrap repair points with yellow adhesive tape to mark a
performed repair.
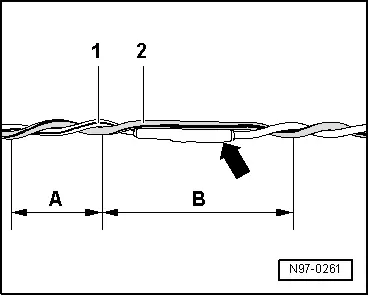
READ NEXT:
Note
The repair of FlexRay wires with coating can only take place
using FlexRay wires with coating from the Parts Catalog.
Observe general notes for repairs on the vehicle electrical
syst
Procedure
- Free up the wire to be repaired approximately 20 cm on both
sides of the repair point.
Caution
Risk of damaging the electrical wires.
Expose wrapped wiring harnesses careful
Caution
Do not bend the fiber-optic cable too much. The
bending radius must be no less than 25 mm.
Fiber optic cables must not be routed over sharp
edges.
The fiber-optic cable must not be
SEE MORE:
Removing
- Disconnect the door connector -2-
from the B-pillar. Refer to
→ Electrical Equipment; Rep. Gr.97; Connectors.
- Tape off the B-pillar in the door arrester area using
adhesive tape, so that the paint will not be damaged.
- Remove the bolt -1- for the
doo
Removing
- Turn the light switch to position "0".
- Remove the light switch trim. Refer to
→ Body Interior; Rep. Gr.70; Instrument Panel; Light Switch
Trim, Removing and Installing.
- If equipped, remove the bolts -1 and
4-.
- Release the retainers in the dire